關(guān)于液化天然氣罐車罐體脆裂及磁翻板液位計泄露問題分析
返回列表發(fā)布日期:2019-06-21 10:56:19 |
摘 要 :某單位一液化天然氣罐車罐體發(fā)生泄漏,檢查發(fā)現(xiàn)罐體后封頭外殼局部脆裂。文中通過宏觀檢查、化學(xué)成分分析、金相檢驗、無損檢測、氣密性試驗等技術(shù)手段進行分析,提出外殼局部脆裂是由于磁翻板液位計氣相管接管與管座接頭連接焊縫處斷裂,導(dǎo)致低溫液化天然氣泄漏所致,而接管斷裂是在雙向彎曲應(yīng)力作用下產(chǎn)生疲勞裂紋并擴展所致。最后 , 提出了事故的有效預(yù)防措施。某單位一臺 LNG 罐車在加氣站卸液時,罐車罐體后封頭外殼下部局部脆裂(見圖 1),引起天然氣泄漏事故。受委托,筆者對其開展事故分析。
該罐車的產(chǎn)品型號為 HDS9405GDY,制造日期為2015 年 2 月,所有連接管線開孔集中在后封頭下部,主要技術(shù)參數(shù)見表 1。
1 技術(shù)分析
1.1 宏觀檢查
將后封頭外殼局部解體,經(jīng)宏觀檢查,內(nèi)筒后封頭無可見變形,從圖 1 觀察可發(fā)現(xiàn),外殼后封頭開裂其裂口均源自接管與封頭外殼角焊縫處。外殼后封頭裂塊及氣相管、管座形貌見圖 2,觀察可見其外殼后封頭破裂斷口無任何塑性變形,呈現(xiàn)典型脆性斷裂特征。接管與內(nèi)筒角焊縫無表面缺陷。磁翻板液位計氣相接管與外筒管座連接處發(fā)生斷裂。
氣相接管宏觀斷口形貌見圖 3,該斷口宏觀上無塑性變形痕跡 , 有兩個特點鮮明的區(qū)域:
1)裂紋源區(qū):裂源有兩處,分別位于氣相接管斷口對側(cè),處于上下方位,出現(xiàn)在氣相接管角焊縫熔合區(qū),見圖 3 箭頭所指;
2)裂紋擴展區(qū) ( 疲勞區(qū) ):該區(qū)域具有明顯的海灘狀或貝紋狀花紋,占有較大面積 , 代表裂紋前沿擴展遺留下的痕跡,逆指向裂紋源。由于裂紋擴展區(qū) ( 疲勞區(qū) ) 所占面積大 , 說明裂紋緩慢擴展形成斷裂面 ,而最后斷裂區(qū)域面積小 , 說明造成該氣相接管斷裂的載荷較小。
由上述斷口特征可知 , 該氣相接管屬疲勞斷裂,斷口對側(cè)兩處疲勞源說明它在服役過程中受到罐車行駛過程氣相接管上下振動引起的附加彎矩作用下的拉壓循環(huán)應(yīng)力作用。而裂紋擴展區(qū) ( 疲勞區(qū) ) 所占面積大說明造成疲勞的載荷較小。
1.2 化學(xué)成分分析
經(jīng)查閱罐車原始技術(shù)資料,氣相接管材料牌號為S30408,材料標(biāo)準(zhǔn)為 GB 24511—2009《承壓設(shè)備用不銹鋼鋼板及鋼帶》;罐體外殼材料牌號為 Q345R,材料標(biāo)準(zhǔn)為GB 713—2008《鍋爐和壓力容器用鋼板》。
1)磁翻板液位計氣相接管材料化學(xué)成份分析結(jié)果見表 2。
1.3 金相檢驗
1)取樣位置及金相試樣:取樣部位示意圖見圖 4,金相試樣見圖 5。
2)金相檢驗結(jié)果
(1)氣相接管基體金相組織:氣相接管基體金相組織見圖 6,其金相組織為單一奧氏體,為 304 奧氏體不銹鋼在正常固溶狀態(tài)下的組織;
(2)氣相接管與接頭焊接處的金相組織:
① 接接頭處的金相組織見圖 7、圖 8。由圖 7、圖8 可見,在焊縫根部產(chǎn)生向氣相接管內(nèi)部擴展(見圖 7)和向焊縫內(nèi)部擴展(見圖 8) 的微裂紋 , 該處正好位于焊接應(yīng)力集中處。
② 裂源處金相組織:裂源處的金相組織見圖 9,由圖 9 可見該處氣相接管組織存在大量滑移線,表明該處已經(jīng)產(chǎn)生塑性變形。
(3)氣相接管外表面質(zhì)量缺陷:圖 10 是氣相接管外表面的金相組織。由圖 10 可見,外表面存在有向基體內(nèi)延伸的微裂紋,且不止一處。圖 11 顯示同樣的質(zhì)量缺陷。從裂紋形貌分析 , 這種外表面微裂紋為鋼管軋制過程中的表面刮傷。
1.4 無損檢測
由于接管與內(nèi)筒體連接角焊縫易產(chǎn)生未焊透及未熔合等缺陷,導(dǎo)致裂紋等穿透性缺陷產(chǎn)生,對內(nèi)筒與接管所有角焊縫采用 100% 滲透檢測,未發(fā)現(xiàn)缺陷痕跡顯示。
1.5 氣密性試驗
封閉斷裂磁翻板液位計氣相管,罐體內(nèi)筒進行氣密性試驗;試驗壓力為 0.7MPa,保壓 30min,罐體無泄漏,無異常響聲,試驗合格,無其他泄漏點。
2 綜合分析及結(jié)論
2.1 外殼破裂原因
外筒所用材料 Q345R 屬于體心立方晶格,該類金屬材料在脆性轉(zhuǎn)變溫度區(qū)域以上,金屬材料處于韌性狀態(tài),斷裂形式主要為韌性斷裂;在脆性轉(zhuǎn)變溫度區(qū)域以下,材料處于脆性狀態(tài),斷裂形式主要為脆性斷裂。經(jīng)查閱原始技術(shù)資料,罐體外筒焊縫未進行消除應(yīng)力熱處理,因此接管與封頭角焊縫存在較大焊接殘余應(yīng)力。
由于磁翻板液位計氣相接管(材質(zhì):S30408,規(guī)格:φ 12×3mm)與管座接頭(材質(zhì):S30408 Ⅲ,規(guī)格:φ 26×6mm)焊縫接管側(cè)熔合線處斷裂(見圖 3),低溫液化天然氣液體及氣體同時從破裂處進入真空夾層,同時低溫液體迅速汽化,造成夾層真空度破壞,真空度破壞后真空閥脫落,真空夾層與大氣聯(lián)通,真空夾層承受的壓力為 0MPa。罐體外筒材料 Q345R 無塑性轉(zhuǎn)變溫度(NDTT)為 -30℃,低溫天然氣工作溫度 -162℃,低溫天然氣長時間與外筒接觸,導(dǎo)致氣相接管斷裂處附近外殼金屬溫度遠遠低于無塑性轉(zhuǎn)變溫度,材料處于脆性狀態(tài),在接管角焊縫殘余應(yīng)力作用下使外殼體局部產(chǎn)生低溫脆性破裂。
2.2 氣相接管斷裂原因
由 于 液 位 計 氣 相 接 管 直 徑 較 小、 壁 厚 較 ?。?φ 12×3mm)且長度較長,設(shè)計中未采用有效方法固定,在車輛行駛過程中氣相接管產(chǎn)生較大振動,此振動在氣相接管與管座角焊縫處形成頻率很高的附加彎矩產(chǎn)生的拉壓循環(huán)應(yīng)力,是產(chǎn)生疲勞裂紋的主要應(yīng)力源,此外該位置還存在焊接殘余應(yīng)力及溫差應(yīng)力,這些應(yīng)力共同作用產(chǎn)生疊加拉壓循環(huán)應(yīng)力,而氣相接管與管座角焊縫處由于幾何形狀突變產(chǎn)生嚴重的應(yīng)力集中,同時斷裂位置處于焊接熔合線處,該處具有明顯的化學(xué)成分不均勻及組織不均勻性,其組織特征為粗大的過熱組織,機械性能較差,因而疲勞裂紋極易在該處形成并擴展。通過斷口金相分析,斷口形式為附加彎矩產(chǎn)生的拉壓疲勞斷裂,由圖10及圖11分析結(jié)果,氣相管表面存在有向基體內(nèi)延伸的微裂紋,該微裂紋成為疲勞裂紋的裂紋源。該位置在疊加的拉壓循環(huán)應(yīng)力作用下產(chǎn)生疲勞裂紋并擴展最后造成接管斷裂。
3 結(jié)論及預(yù)防措施
1)氣相接管表面存在有向基體內(nèi)延伸的微裂紋,該微裂紋成為疲勞裂紋的裂紋源;由于罐車運行過程氣相接管振動在接管與管座角焊縫部位產(chǎn)生附加彎矩引起的拉壓循環(huán)應(yīng)力,該應(yīng)力與焊接殘余應(yīng)力及溫差應(yīng)力疊加作用在該部位產(chǎn)生疲勞裂紋并擴展最后造成接管斷裂。
2)氣相接管斷裂后,天然氣低溫液體及氣體從裂口進入真空夾層,逸出的低溫天然氣長時間與外筒接觸,導(dǎo)致氣相接管斷裂處附近外殼金屬溫度遠遠低于無塑性轉(zhuǎn)變溫度,材料處于脆性狀態(tài),在接管角焊縫殘余應(yīng)力作用下使外殼體局部產(chǎn)生低溫脆性破裂。
3)磁翻板液位計接管采用表面質(zhì)量更好的不銹鋼管制造,避免鋼管表面原始微裂紋的產(chǎn)生,同時裝配焊接時避免強力組裝,提高角焊縫焊接質(zhì)量;
4)JB/T 4783—2007《低溫液體汽車罐車》第4.4.16.4 款規(guī)定:“管路系統(tǒng)的設(shè)計、制造和安裝應(yīng)避免熱脹冷縮、機械顫動或振動等所引起的損壞,必要時應(yīng)考慮補償裝置……”。因此必須按照標(biāo)準(zhǔn)要求改進磁翻板液位計接管設(shè)計,增設(shè)接管穩(wěn)定裝置,減少車體運行時接管的震動,減少振動應(yīng)力。
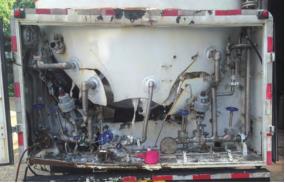
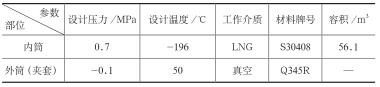
1.1 宏觀檢查
將后封頭外殼局部解體,經(jīng)宏觀檢查,內(nèi)筒后封頭無可見變形,從圖 1 觀察可發(fā)現(xiàn),外殼后封頭開裂其裂口均源自接管與封頭外殼角焊縫處。外殼后封頭裂塊及氣相管、管座形貌見圖 2,觀察可見其外殼后封頭破裂斷口無任何塑性變形,呈現(xiàn)典型脆性斷裂特征。接管與內(nèi)筒角焊縫無表面缺陷。磁翻板液位計氣相接管與外筒管座連接處發(fā)生斷裂。
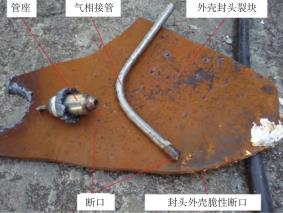
1)裂紋源區(qū):裂源有兩處,分別位于氣相接管斷口對側(cè),處于上下方位,出現(xiàn)在氣相接管角焊縫熔合區(qū),見圖 3 箭頭所指;
2)裂紋擴展區(qū) ( 疲勞區(qū) ):該區(qū)域具有明顯的海灘狀或貝紋狀花紋,占有較大面積 , 代表裂紋前沿擴展遺留下的痕跡,逆指向裂紋源。由于裂紋擴展區(qū) ( 疲勞區(qū) ) 所占面積大 , 說明裂紋緩慢擴展形成斷裂面 ,而最后斷裂區(qū)域面積小 , 說明造成該氣相接管斷裂的載荷較小。
由上述斷口特征可知 , 該氣相接管屬疲勞斷裂,斷口對側(cè)兩處疲勞源說明它在服役過程中受到罐車行駛過程氣相接管上下振動引起的附加彎矩作用下的拉壓循環(huán)應(yīng)力作用。而裂紋擴展區(qū) ( 疲勞區(qū) ) 所占面積大說明造成疲勞的載荷較小。
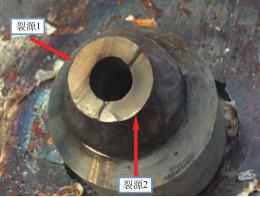
經(jīng)查閱罐車原始技術(shù)資料,氣相接管材料牌號為S30408,材料標(biāo)準(zhǔn)為 GB 24511—2009《承壓設(shè)備用不銹鋼鋼板及鋼帶》;罐體外殼材料牌號為 Q345R,材料標(biāo)準(zhǔn)為GB 713—2008《鍋爐和壓力容器用鋼板》。
1)磁翻板液位計氣相接管材料化學(xué)成份分析結(jié)果見表 2。
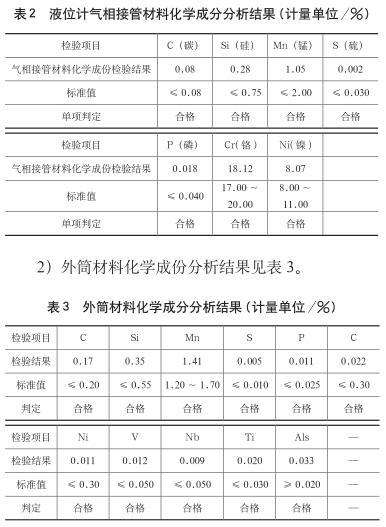
1)取樣位置及金相試樣:取樣部位示意圖見圖 4,金相試樣見圖 5。
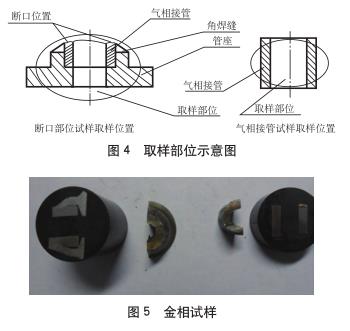
(1)氣相接管基體金相組織:氣相接管基體金相組織見圖 6,其金相組織為單一奧氏體,為 304 奧氏體不銹鋼在正常固溶狀態(tài)下的組織;
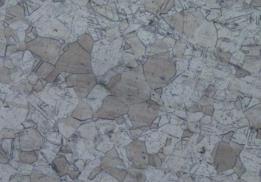
① 接接頭處的金相組織見圖 7、圖 8。由圖 7、圖8 可見,在焊縫根部產(chǎn)生向氣相接管內(nèi)部擴展(見圖 7)和向焊縫內(nèi)部擴展(見圖 8) 的微裂紋 , 該處正好位于焊接應(yīng)力集中處。
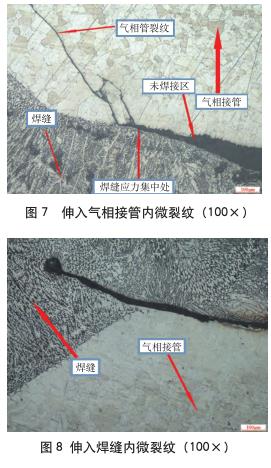
(3)氣相接管外表面質(zhì)量缺陷:圖 10 是氣相接管外表面的金相組織。由圖 10 可見,外表面存在有向基體內(nèi)延伸的微裂紋,且不止一處。圖 11 顯示同樣的質(zhì)量缺陷。從裂紋形貌分析 , 這種外表面微裂紋為鋼管軋制過程中的表面刮傷。
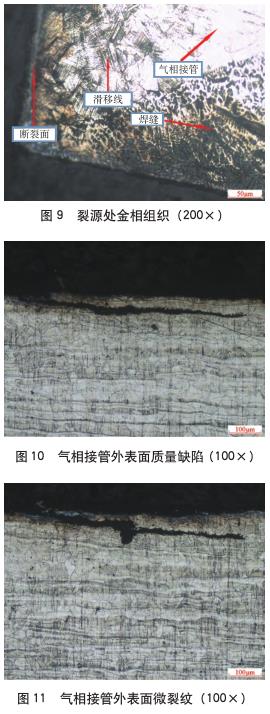
由于接管與內(nèi)筒體連接角焊縫易產(chǎn)生未焊透及未熔合等缺陷,導(dǎo)致裂紋等穿透性缺陷產(chǎn)生,對內(nèi)筒與接管所有角焊縫采用 100% 滲透檢測,未發(fā)現(xiàn)缺陷痕跡顯示。
1.5 氣密性試驗
封閉斷裂磁翻板液位計氣相管,罐體內(nèi)筒進行氣密性試驗;試驗壓力為 0.7MPa,保壓 30min,罐體無泄漏,無異常響聲,試驗合格,無其他泄漏點。
2 綜合分析及結(jié)論
2.1 外殼破裂原因
外筒所用材料 Q345R 屬于體心立方晶格,該類金屬材料在脆性轉(zhuǎn)變溫度區(qū)域以上,金屬材料處于韌性狀態(tài),斷裂形式主要為韌性斷裂;在脆性轉(zhuǎn)變溫度區(qū)域以下,材料處于脆性狀態(tài),斷裂形式主要為脆性斷裂。經(jīng)查閱原始技術(shù)資料,罐體外筒焊縫未進行消除應(yīng)力熱處理,因此接管與封頭角焊縫存在較大焊接殘余應(yīng)力。
由于磁翻板液位計氣相接管(材質(zhì):S30408,規(guī)格:φ 12×3mm)與管座接頭(材質(zhì):S30408 Ⅲ,規(guī)格:φ 26×6mm)焊縫接管側(cè)熔合線處斷裂(見圖 3),低溫液化天然氣液體及氣體同時從破裂處進入真空夾層,同時低溫液體迅速汽化,造成夾層真空度破壞,真空度破壞后真空閥脫落,真空夾層與大氣聯(lián)通,真空夾層承受的壓力為 0MPa。罐體外筒材料 Q345R 無塑性轉(zhuǎn)變溫度(NDTT)為 -30℃,低溫天然氣工作溫度 -162℃,低溫天然氣長時間與外筒接觸,導(dǎo)致氣相接管斷裂處附近外殼金屬溫度遠遠低于無塑性轉(zhuǎn)變溫度,材料處于脆性狀態(tài),在接管角焊縫殘余應(yīng)力作用下使外殼體局部產(chǎn)生低溫脆性破裂。
2.2 氣相接管斷裂原因
由 于 液 位 計 氣 相 接 管 直 徑 較 小、 壁 厚 較 ?。?φ 12×3mm)且長度較長,設(shè)計中未采用有效方法固定,在車輛行駛過程中氣相接管產(chǎn)生較大振動,此振動在氣相接管與管座角焊縫處形成頻率很高的附加彎矩產(chǎn)生的拉壓循環(huán)應(yīng)力,是產(chǎn)生疲勞裂紋的主要應(yīng)力源,此外該位置還存在焊接殘余應(yīng)力及溫差應(yīng)力,這些應(yīng)力共同作用產(chǎn)生疊加拉壓循環(huán)應(yīng)力,而氣相接管與管座角焊縫處由于幾何形狀突變產(chǎn)生嚴重的應(yīng)力集中,同時斷裂位置處于焊接熔合線處,該處具有明顯的化學(xué)成分不均勻及組織不均勻性,其組織特征為粗大的過熱組織,機械性能較差,因而疲勞裂紋極易在該處形成并擴展。通過斷口金相分析,斷口形式為附加彎矩產(chǎn)生的拉壓疲勞斷裂,由圖10及圖11分析結(jié)果,氣相管表面存在有向基體內(nèi)延伸的微裂紋,該微裂紋成為疲勞裂紋的裂紋源。該位置在疊加的拉壓循環(huán)應(yīng)力作用下產(chǎn)生疲勞裂紋并擴展最后造成接管斷裂。
3 結(jié)論及預(yù)防措施
1)氣相接管表面存在有向基體內(nèi)延伸的微裂紋,該微裂紋成為疲勞裂紋的裂紋源;由于罐車運行過程氣相接管振動在接管與管座角焊縫部位產(chǎn)生附加彎矩引起的拉壓循環(huán)應(yīng)力,該應(yīng)力與焊接殘余應(yīng)力及溫差應(yīng)力疊加作用在該部位產(chǎn)生疲勞裂紋并擴展最后造成接管斷裂。
2)氣相接管斷裂后,天然氣低溫液體及氣體從裂口進入真空夾層,逸出的低溫天然氣長時間與外筒接觸,導(dǎo)致氣相接管斷裂處附近外殼金屬溫度遠遠低于無塑性轉(zhuǎn)變溫度,材料處于脆性狀態(tài),在接管角焊縫殘余應(yīng)力作用下使外殼體局部產(chǎn)生低溫脆性破裂。
3)磁翻板液位計接管采用表面質(zhì)量更好的不銹鋼管制造,避免鋼管表面原始微裂紋的產(chǎn)生,同時裝配焊接時避免強力組裝,提高角焊縫焊接質(zhì)量;
4)JB/T 4783—2007《低溫液體汽車罐車》第4.4.16.4 款規(guī)定:“管路系統(tǒng)的設(shè)計、制造和安裝應(yīng)避免熱脹冷縮、機械顫動或振動等所引起的損壞,必要時應(yīng)考慮補償裝置……”。因此必須按照標(biāo)準(zhǔn)要求改進磁翻板液位計接管設(shè)計,增設(shè)接管穩(wěn)定裝置,減少車體運行時接管的震動,減少振動應(yīng)力。